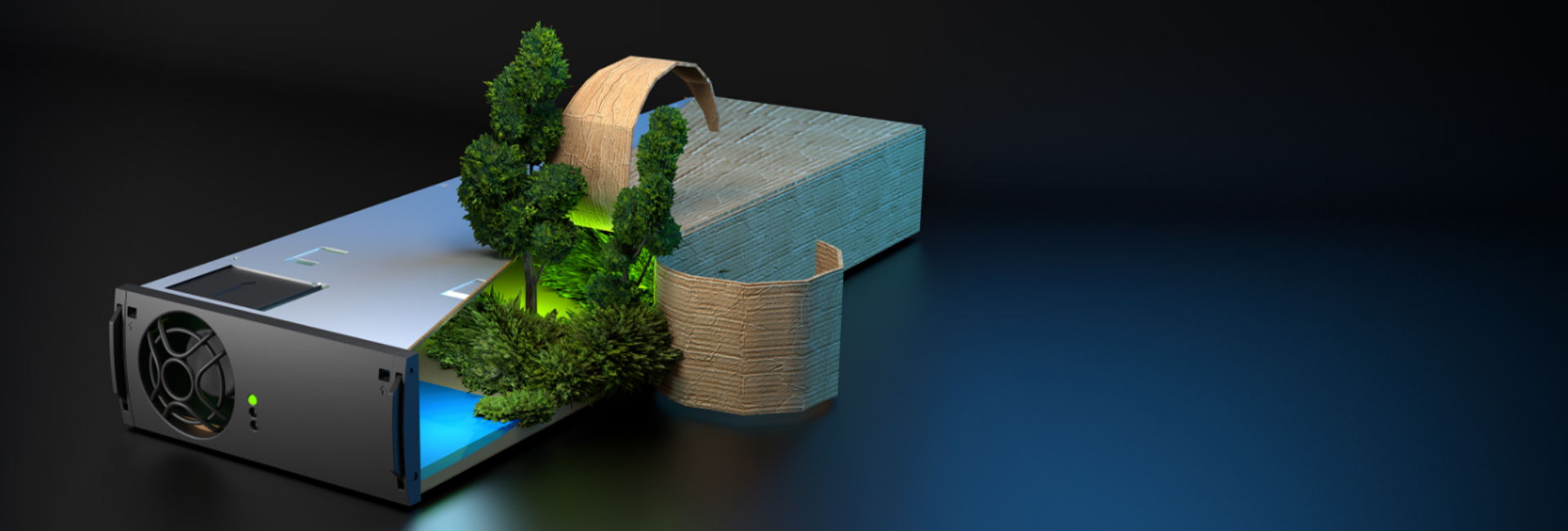
In depth
Packed with care
Designing for sustainability
Many of Eltek’s high-volume products are manufactured in Asia. They are shipped directly or via regional and local warehouses and assembly sites to each individual customer. During this limited period of the product’s lifetime, the packaging plays a very important role. It takes on a life of its own.
A denser future
It is on the designers’ big screens that new products first can be seen, in various stages of the development process, from early conceptual sketches to detailed 3D representations of the finished product. Christine Amer-Tjade is the lead industrial designer at Eltek’s corporate R&D department in Norway, and she combines her passion for functional and appealing product design with an equally passionate interest in what first meets the customer’s eyes: the packaging around the product.
The packaging is a significant part of the product. It provides protection and makes the product transportable and storable. But it also has an environmental aspect, in terms of resource usage and waste handling. “The packaging is very much part of the solution we deliver, and we put a lot of consideration into its design. The basic function of providing proper protection for the valuable product it houses, is of course main priority. In addition, we aim for the highest possible efficiency in the handling of packaged goods. This means considering factors such as size, weight and volume carefully.
Last, but not least, we design packaging with the environment in mind. The good thing is that all these considerations reinforce each other and contribute in the same direction, towards a common goal – the most efficient and sustainable packaging”, Christine explains.
“Our pledge to substantially reduce use of plastics is part of our environmental responsibility. We have a commitment to sustainability in everything we do.”
Christine Amer-Tjade
Packaging pays back
Being a global company with both high-volume products and bulky systems, freight is a significant cost element with a substantial impact on the bottom line. Packaging plays a key role in Eltek’s ongoing efforts to reduce logistics cost. “We think long and hard about how to design our packaging with respect to its efficiency, i.e. its impact on the cost of freight, storage and handling, throughout the chain from manufacturing to installation and use. It is obvious that packaging is important. In one project, we redesigned the packaging, reducing its volume and weight, while ensuring efficient stacking on EUR pallets and in containers. As a result, we reduced freight costs by 40 %, and not counting the environmental benefits”, Christine explains.
Getting rid of plastic
Eltek has embarked on a program with the aim of substantially reducing oil-based materials, i.e. plastics, used in the packaging, as well as in the products themselves, while maintaining important product properties and low weight.
“The oceans are filling up with plastics. This has opened the world’s eyes to a problem of a magnitude we have just begun to comprehend. Plastics constitute a serious threat to the entire global environment, not only the oceans. At current date plastics are not yet sustainable enough regarding material composition or recyclability to be used without thorough consideration. Our pledge to substantially reduce use of plastics is part of our environmental responsibility. We have a commitment to sustainability in everything we do”, says Christine.
One very specific measure is to replace the plastic that is used for cushioning the product in its box. “We are replacing the polystyren and polyethylene with corrugated cardboard. Unlike plastic, it is compostable. This means that when you return it to nature, it will decompose and return to a natural state – unlike plastics, which may be biodegradable, but only into small pieces of plastic, known as microplastics.
Corrugated cardboard also has very good recycling properties, and there are well-established recycling schemes in place in most countries. Corrugated cardboard can be recycled seven times, before the fibers become too short and get washed out of the mix”, says Christine.
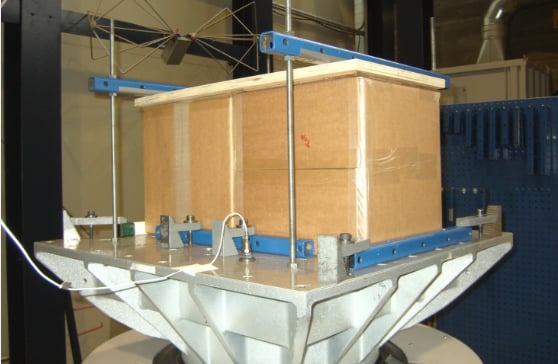
The vibration test is performed with boxes, including products, mounted on top of a vibrator by means of a 20 mm laminated wooden plate and yokes. The boxes are rotated and tested in all three axis.
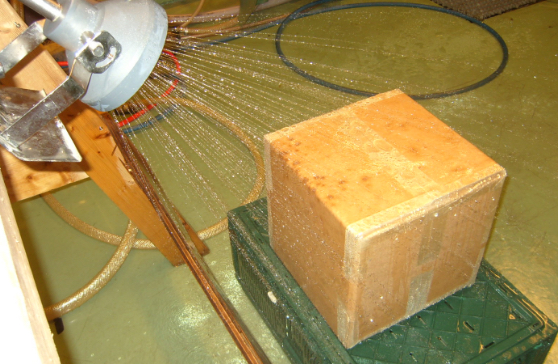
During the water test, the boxes, including products, are exposed to “rain”. The boxes are turned around after 7,5 min x 4 to equally distribute water on each side of the box.
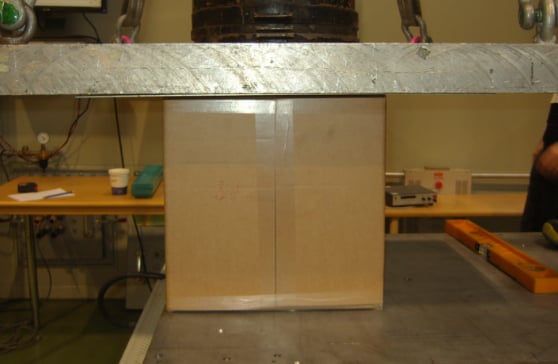
The mechanical strength test is perfomed when the package is loaded with deadweight in steps of 15 kg up to100 kg to simulate transport conditions.
Putting packaging to the test
Sufficient cushioning is an absolute requirement. An important part of the process is to test the solidness of the packaging. To make sure, the packaging is made subject to rough handling. With its precious content in place, either prototypes or finished products, the packaging is drop tested in accordance with international certification standards.
These prescribe the box being dropped 13 times in a specific manner and order, targeting corners, edges and surfaces, from one meter height (products with weight above 20 kg have other criteria). The damage to packaging and possibly the products is evaluated after the 1st and 13th drop. The packaging is then either approved or altered to find the perfect fit between probability for drop and damage against cost of extra cushioning or unnecessary wrapping. Water resistance is another quality subject to testing.
Many pennies make a pound
Concern for the environment takes many shapes. Every small step matters. One good thing about most initiatives, is that they also save money and are business-wise in their own right.
One example of such a “good for business/good for the environment” measure, is found at Eltek’s test facilities, where products are “burnt-in”, i.e. tested before their release to the market, under tougher conditions than they will ever meet in real life.
By redesigning the test environment, using modified proprietary inverter technology from the development lab, power consumption used for testing has been reduced by 50 %. This represents real money and a real reduction of the environmental footprint related to the test procedures.
The design process
Packaging design starts early and goes hand in hand with the rest of the design process. By handling all design issues in parallel, we avoid surprises and awkward solutions because of the need to compensate for problems created by design decisions made early in the process. The integrated approach requires close cooperation with the manufacturers of both the packaging and the products.